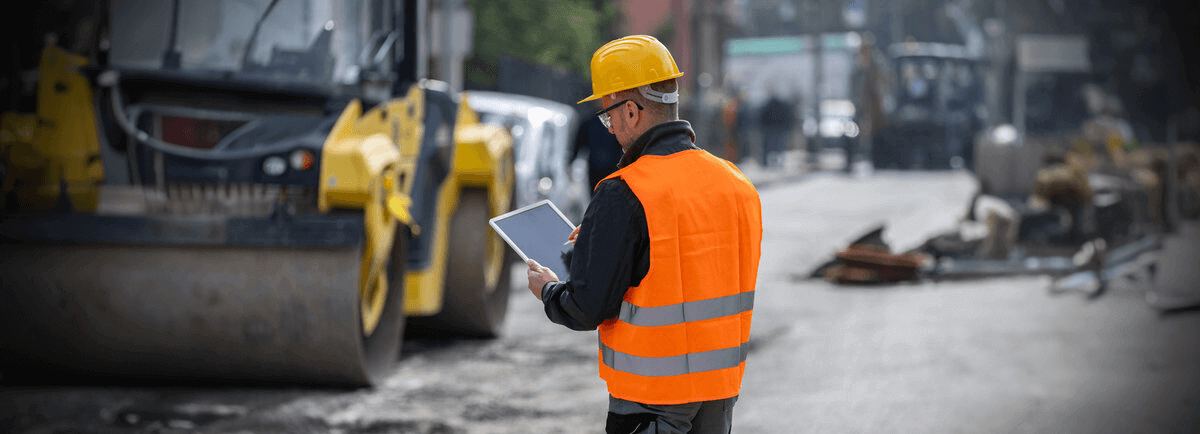
Workplace Incident Management Process: A Step-by-Step Guide
What happens after a workplace accident? Most people have no idea—and honestly, many organizations don’t either.
Incidents can unfold in seconds. A misstep on a ladder. A dropped tool. A chemical spill. But how you respond over the next few hours and days? That’s what truly defines your safety culture.
In my experience, too many companies treat incident management as an afterthought—something you scramble through when something goes wrong. But a clear, repeatable process? That’s how you protect your people, stay compliant, and prevent the next one from happening.
This guide breaks down the incident management process into simple, actionable steps—so you’re ready when it matters most.
What Is a Workplace Incident?
A workplace incident is any unplanned event that disrupts normal operations, causes injury, or creates a safety risk. It doesn’t always have to involve injury—near-misses and unsafe conditions count too.
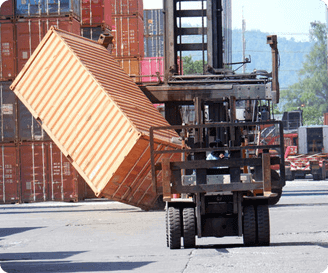
Some examples:
- A forklift collision in the warehouse
- A worker fainting due to heat exposure
- A fire alarm triggered by a short circuit
- Even a close call where someone almost gets hurt
Ignoring these events is risky. They’re early warning signs that something in your system isn’t working—and they deserve attention.
Why a Process Matters
Without a defined process, people guess. Some don’t report incidents at all. Others might skip critical steps in the rush to get back to work. That leads to:
- Recurring incidents
- Legal trouble
- Poor safety culture
- And honestly, stressed-out safety teams
A structured process ensures everyone knows what to do—and does it fast, clearly, and thoroughly.
The 7 Steps of Incident Management
Here’s how a strong workplace incident management process typically flows:
1. Incident Reporting
It starts with awareness. The moment an incident occurs, it should be reported—immediately.
Whether it’s through a digital app, an online form, or a physical logbook, what matters is accessibility. Make it easy for workers to report incidents without fear or friction.
Tip: Train your team to report everything, not just injuries. Near-misses and hazards are just as important.
2. Initial Response
Safety first. Once an incident is reported, secure the area to prevent further harm. That might mean stopping equipment, administering first aid, or evacuating a section of the workplace.
At this stage, the goal is simple: protect people and contain the situation.
3. Investigation
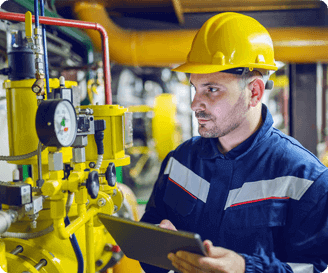
Once the immediate danger has passed, it’s time to dig into what happened.
Interview witnesses. Review CCTV footage if available. Take photographs of the scene. The investigation should be prompt but thorough. Delays lead to lost details.
Assign someone neutral—ideally from the safety team or an authorized investigator. Their job is to collect facts, not place blame.
4. Root Cause Analysis
Now we ask: Why did this really happen?
Root cause analysis helps you get past surface-level explanations (“the worker was careless”) and understand system failures (“no protective barrier in place”).
Common techniques:
- 5 Whys
- Fishbone (Ishikawa) Diagrams
- Fault Tree Analysis
In my experience, this step is where many companies cut corners. But without it, you’re just guessing—and that rarely leads to improvement.
5. Corrective & Preventive Actions (CAPA)
Once the root cause is clear, decide on actions to fix it—and make sure it doesn’t happen again.
There are two types of actions:
- Corrective: Fixing the immediate issue (e.g., replacing broken equipment)
- Preventive: Long-term changes (e.g., redesigning the workflow or retraining staff)
Assign responsibilities, set deadlines, and follow up. A plan without accountability is just paperwork.
6. Documentation & Compliance Reporting
Every incident should be documented—even if it’s minor. This protects your company legally and helps spot patterns over time.
Depending on your location and industry, you may also need to report certain incidents to regulatory bodies (like OSHA in the U.S.).
Keep records organized, accessible, and audit-ready.
7. Follow-Up & Closure
Once all actions are completed, review the outcome.
- Did the corrective actions work?
- Were all tasks completed on time?
- Has the risk been eliminated or minimized?
Only then should the incident be marked as closed. Consider sharing lessons learned internally—it builds a stronger safety culture and prevents recurrence.
Common Mistakes to Avoid
Let’s be real—incident management isn’t always smooth. Here are a few traps I’ve seen teams fall into:
- Delayed reporting: By the time you investigate, the details are fuzzy
- Skipping root cause analysis: You fix the symptom, not the source
- No follow-up: Actions are assigned but never closed
- Blame culture: People stay silent out of fear, and risks go unreported
A good system avoids all of these with transparency, consistency, and trust.
How Software Can Make This Easier
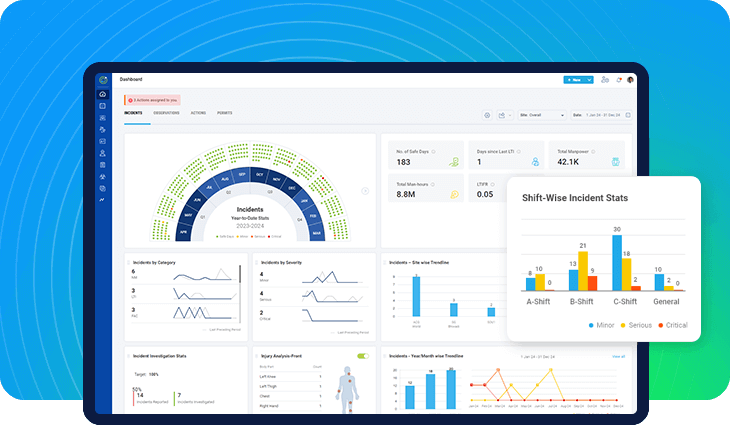
Managing the entire process manually—via forms, spreadsheets, or emails—can quickly become chaotic, especially when you’re juggling multiple incidents, deadlines, and compliance requirements.
That’s where the Safetymint Incident Management System steps in.
It’s a robust solution designed to help you streamline every stage of the incident lifecycle—from reporting to resolution. Whether you’re in construction, manufacturing, healthcare, or utilities, Safetymint brings structure, speed, and accountability to your safety efforts.
Key features of Safetymint IM system include:
- Easy incident reporting via web and mobile (Android & iOS)
- Customizable workflows, fields, and forms to match your process
- Root cause analysis tools, CAPA tracking, and investigation templates
- Real-time dashboards and detailed reports
- Notifications and reminders to stay on top of actions
- Secure and scalable—available as both SaaS and on-premise
Plus, Safetymint is built to adapt. Whether you’re a mid-size factory or a multi-site enterprise, the system can be tailored to fit your operational and regulatory needs.
To learn more, take a 14-day free trial.
This article was generated with the assistance of AI and reviewed by Ramesh Nair for accuracy and quality.
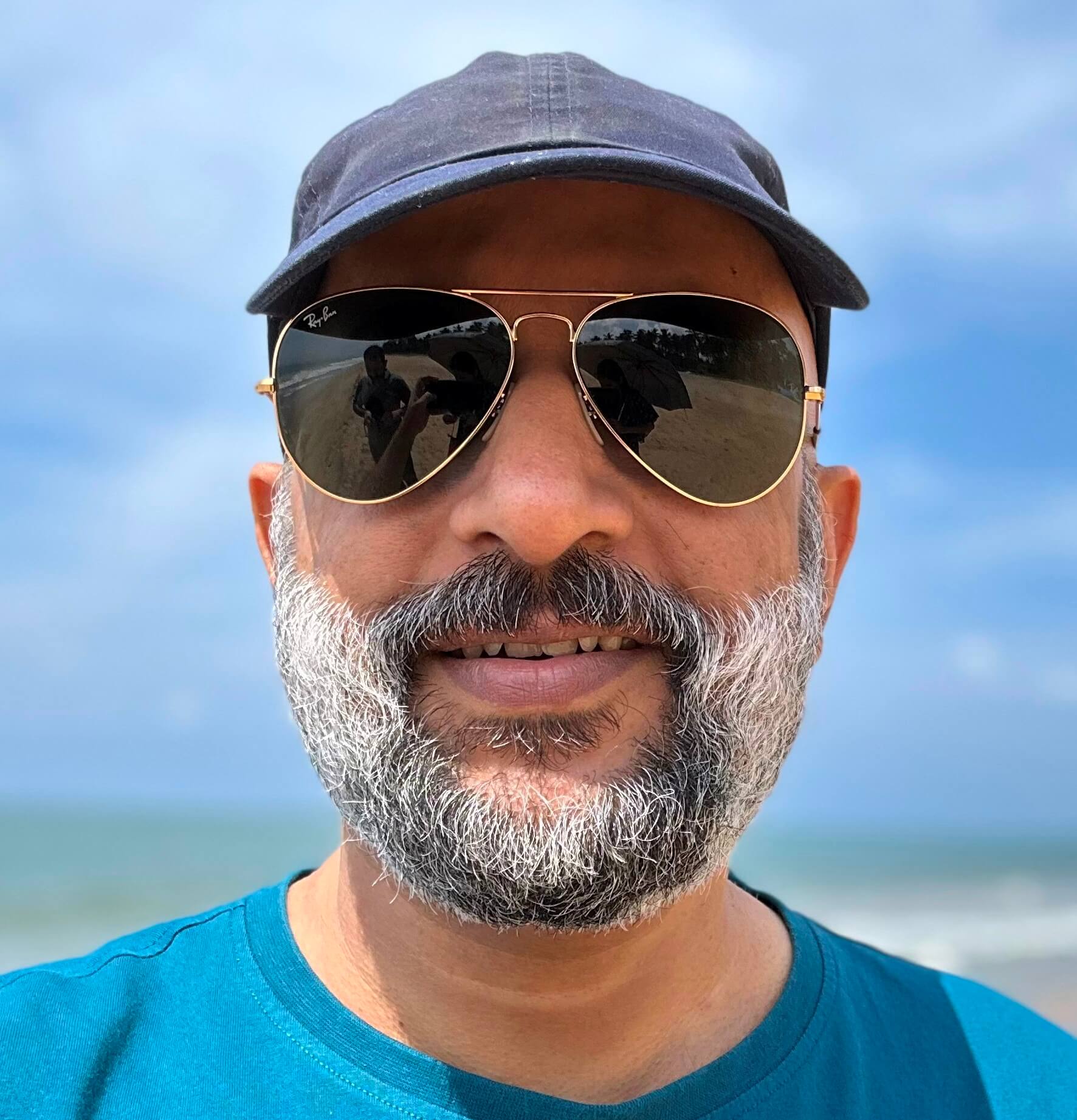
Ramesh Nair is the Founder and Principal Partner of Niyati Technologies, the company behind Safetymint.
He’s a dedicated advocate for workplace safety. Ramesh firmly believes that every individual deserves to return home safely after a day’s work. Safetymint, the innovative safety management software, emerged from this conviction. It’s a platform designed to streamline safety management, empower safety professionals, and enhance safety in workplaces.
Through his blog, Ramesh shares insights, best practices, and innovative solutions for workplace safety. Visit his social media profiles to follow him for regular updates.